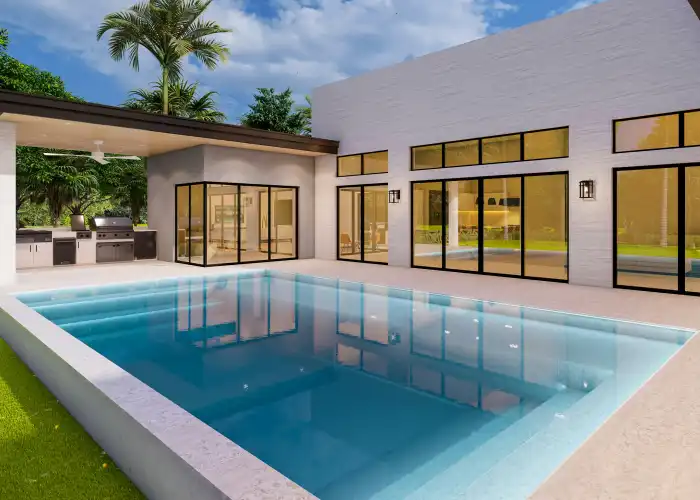
Can I DIY Install a Prefab Pool or Must I Hire Professionals?
The prefab pool installation can appear easy enough: excavate a hole, insert the shell, connect the plumbing, and you're ready to take a swim. But a common question arises: Can I install the prefab pool myself, or should I hire the services of professionals? DIY installation of a pool may seem like a cost-effective decision, but it is linked to heavy lifting, accuracy, and the use of proper tools. The process is more complicated than it seems, whether you are excavating or doing the plumbing.
In this article, we will talk about the process, challenges, cost, and choices of installing a prefab pool. It will give you a fair perspective of whether to do it yourself or hire a professional.
The DIY Installation Process—Detailed Walkthrough
The DIY pool installation may be an exciting idea initially, particularly when the prefab models are delivered pre-formed. Nevertheless, this procedure demands attention to detail, accurate scales, and the appropriate tools. To give you a better idea of what usually goes into a DIY fiberglass prefab pool installation, here is a step-by-step process.
1. Planning and Permissions
Before any digging starts, you’ll need to do the groundwork—on paper.
Local regulations: The installation of pools in most towns or councils will need permits. You will have to communicate with your local authority and perhaps provide a site plan.
Utility checks: Dial before you dig. Pipes or cables in the ground may bring severe delays, risk, or expense.
Soil testing: When working on a slope or unstable ground, it is usually a good idea to find out what kind of ground you are dealing with.
2. Excavation
This is often the most labor-intensive part of the process.
Tools needed: The majority of people rent a small excavator or hire someone specifically to do this step. You must excavate a hole that is a little bit larger and deeper than the pool shell so that you can backfill and level it.
Manual digging: When you are doing a pool manually, it is going to be a huge task. According to several contractors, hand-digging a small pool can take 80 to 100 hours.
Proper leveling: An improperly levelled base will mean that the shell will not fit properly, and this may result in cracking or settling in the future.
According to a study, more than 60% of the failed DIY pool installations are caused by ineffective excavation and levelling.
3. Preparing the Base
Once you’ve dug the hole, a solid base needs to be created.
Material: A crushed stone or gravel is normally applied, and a layer of sand is applied on top to make the fine adjustments.
Laser leveling: A laser level or transit is critical to ensure the base is perfectly flat. Even a slight slope can cause long-term issues.
Compact the base: Use a plate compactor to ensure there’s no loose fill that might shift later.
4. Placing the Pool Shell
The pool shell is delivered in one large piece. This step can be risky without lifting machinery.
The shell normally requires cranes or backhoes to move it up or down safely into the excavated hole.
Unless you have the right equipment, you can easily break the shell when you do this step, or you can hurt yourself.
After setting it in place, the level must be re-checked before proceeding to the next step.
5. Plumbing and Electrical Work
This is the stage where most DIYers struggle.
Pipes and filters: You’ll need to connect the skimmer, return lines, suction lines, and potentially a heating system.
Electricals: Pumps and lights must be connected by a licensed electrician. This isn’t optional; local codes typically demand certified work for safety and insurance reasons.
If done incorrectly, plumbing leaks may not appear until weeks later, requiring you to dig everything back up.
6. Backfilling and Filling
The plumbing is ready and tested; now it is time to backfill the shell.
Balanced filling: As water is added to the pool, backfill material (usually gravel or sand) should be added around the sides at the same pace. This avoids structural pressure imbalances.
Add slowly, stopping often to recheck level and alignment.
Compact lightly to avoid future settling.
7. Coping, Decking, and Finishing
This is the final stretch of your DIY journey.
Coping: Concrete, pavers, or precast coping is placed all around the pool edge to lock everything up and provide a final look.
Decking: Whether it’s concrete, tile, or timber, proper sloping for drainage and non-slip surfaces should be planned.
Fencing: Childproof fencing with self-latching gates is usually required by local laws. For DIY installation, you might need another permit and must be done according to safety codes.
Most homeowners hire prefab pool installers to complete some steps, such as shell installations or plumbing, instead of doing the whole process themselves. This hybrid approach helps manage cost while reducing risk.
Common Pitfalls in DIY Pool Installation
The DIY approach to prefab pool installation can be very satisfying, but some common pitfalls may cause serious setbacks.
Poor Ground Levelling
When the ground is not levelled properly, then the shell of the pool might tilt or not settle properly. This may lead to structural stress, uneven water lines, or cracking. Always use a laser level, not just trust your eyes.
Weak Base Material
Filling the pool with soft material such as dirt or poorly compacted sand may result in the pool moving over time. Long-term stability requires a solid base composed of a dense material (normally compacted gravel with fine sand as a surface layer).
Difficult Shell Placement
Fiberglass shells are cumbersome and bulky. You will be unable to move the shell without a proper lifting tool, like a crane or a backhoe; otherwise, you are likely to break the shell or hurt yourself.
Plumbing Errors
DIY plumbing is tricky. Improper sealing or skipped pressure testing can lead to leaks that may not show up for weeks, and fixing them often means digging everything up again.
Backfilling Too Fast
If you don’t backfill evenly while filling the pool with water, pressure differences can crack or warp the shell.
Ignoring Permits and Codes
Missing fencing, inspections, or permits can lead to fines or failed certifications. Always follow local council regulations.
Can I DIY install a Prefab Pool, or must I hire Professionals?
You may do a DIY installation of a pool, particularly when you are using a prefab fiberglass pool. These pools are a single pre-formed shell, so there is no need to do complicated concrete work. Nevertheless, it is not a simple process, and it requires some technical work that may involve a number of tools, planning, and physical tasks.
DIY Installation Might Work If:
You have access to tools like an excavator or a laser level
You're comfortable reading site plans and using construction equipment.
You’re able to follow local building codes and safety regulations.
You can hire a licensed electrician for pump and light installation.
You have basic plumbing skills, or can get help with this step.
When Hiring Professionals Is Better:
If you're unsure how to level ground or prepare a stable base
If you can’t safely lift or position the pool shell
If you lack experience with plumbing or electrical work
If you want to ensure your pool passes all local inspections
A hybrid approach is the best way to go for most homeowners: they can do things that are easy, such as digging or completing the decking on their own, and hire prefab pool installers where they need more expertise.
FAQs
Can I install a fiberglass pool myself?
Yes, if you have the right gear—excavator, crane—and can manage plumbing and electrical requirements. It could be done, but not easily.
Can you build a pool without an excavator?
For a tiny, shallow pool—yes. However, realistic inground shells need machine excavation. Manual digging consumes 3 -5 weeks or even longer.
How hard is it to build your pool?
Some of the common challenges you may face are access to the site, accurate leveling, reinforcement of the structure, bonding of electrical systems, water systems, and code compliance.
How long would it take to hand-dig a pool?
A 30×15 ft pool can take 3–5 full weeks of effort if the soil is cooperative. Rocky or compact ground increases that timeline.
What is the most expensive part of building a pool
Typically, the shell and excavation. Shells cost $21k–$40k, excavation and machinery another $3k–$10k, often making up over half your build cost.
Conclusion
It is possible to install a prefab pool yourself, but it is not a small weekend-sized project. It requires digging, site preparation, plumbing, electrical services, and legal proceedings, which all need some skill and planning. A DIY installation can be a good, cost-effective solution in case you have experience in home improvement projects, you have the right tools, and you are ready to put effort into it.